Grow Vegetables Like You Mean It
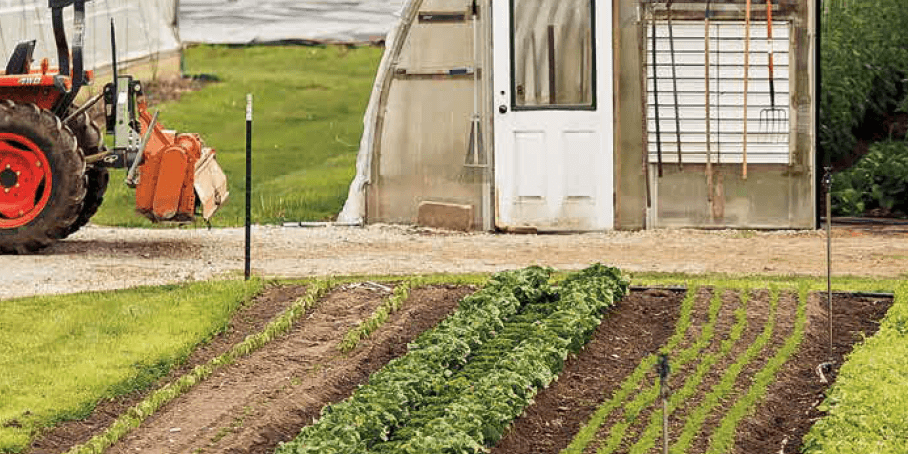
In the United States, 40 percent of the food we produce is wasted. Ben Hartman is trying to put a dent in that dismal statistic. Inspired by Toyota’s “lean” approach to manufacturing, a production strategy designed to minimize waste and maximize efficiency while increasing profits.
In his practical how-to manual, Hartman shows how he has implemented lean thinking in every area of his work. Using the lean system, Hartman is able to earn a comfortable living on just an acre of land while finding life balance at the same time.
The excerpt below is from, The Lean Farm Guide to Growing Vegetables and has been adapted for the web.
In 2011 I received an email from Steve Brenneman, a CSA customer and the owner of an aluminum trailer factory. He had recently transformed his factory using the lean system, a Japanese invention designed to cut out waste and increase profits with less work. Brenneman offered to help us do the same on our farm. After initial skepticism (factory methods on farms haven’t always churned out sustainable outcomes), we took him up on his offer. Over the following several seasons, we proceeded to declutter our workspaces and cut waste from our processes. We now earn a comfortable living from our farm, and neither of us works off the property. We have stable, long-term customers, and our work doesn’t overburden us.
Five core lean principles have benefited us the most. These principles underlie the production systems in this book, and we use them to this day.
- Keep only the tools that add value.
- Let the customer define value.
- Identify the steps that add value.
- Cut out the muda—anything that does not add value.
- Practice kaizen—continuous improvement.
1. KEEP ONLY THE TOOLS THAT ADD VALUE
Lean relies on organization to keep workspaces clean. The most important step is sorting, discarding any item from your workspace that is not used every season to create value. This has not always been easy for us to do. At first we placed too much stock in tools that, realistically, we would never use. Now we have routines for constantly making sure we are surrounded only by what we need.
Farmers love to collect tools and hoard things. But we must check that instinct because everything we keep has a cost. It costs time to trip over shovels and look for hoes. It costs to store items—property taxes on buildings and expenses to maintain those buildings. Plus there is the mental cost of living with clutter. These are costs that suck energy and money without giving anything back besides the vacuous satisfaction of ownership.
2. LET THE CUSTOMER DEFINE VALUE
A second practice underlying our daily work is to always have our customers and their wishes in mind. We are growing food for them, and the products they want, both goods and services, guide our work. Specifically, we seek out answers to these three questions:
- What do our customers want?
- When do they want it?
- What amount do they want?
The more precisely we answer these questions and deliver on the answers, the more profitable we will be at year’s end. To be sure, we don’t fulfill every wish. For example, while customers might love watermelons, we don’t grow them because, for us, they are not profitable. Still, continually posing and answering the three questions ensures that paying customers, not our own whims, steer our farming.
3. IDENTIFY THE STEPS THAT ADD VALUE
The next principle we follow is to carefully trace value. In which steps do tomatoes and peppers and carrots become more valuable? When are we adding to their value, and when are we just spinning wheels? In a factory setting, value might be added when steel is welded to steel. That is the point when each piece is suddenly worth more. On the farm we’ve found that surprisingly few actions—seeding, harvesting, and washing food, for example—build value. These direct actions cause our food to be worth more.
4.CUT OUT THE MUDA—ANYTHING THAT DOES NOT ADD VALUE
According to the lean system, actions on your farm that don’t directly add value—like lawn mowing, cleaning, and leafing through catalogs—are considered muda. The closest English equivalent is “waste.” The Japanese managers who developed the lean system were precise when outlining forms of muda. Here they are as applied to the farm:
- Overproduction—spending resources on products that do not sell
- Waiting—products or people sitting idle
- Unnecessary transportation—too much driving, too little farming
- Overprocessing—washing and packaging more than the customer requires
- Too much inventory—unused supplies or sellable food plugging up the farm
- Unnecessary motion—any physical action that is not creating value
- Making defective products—twisted carrots, wormy tomatoes
- Overburdening (muri)—unreasonable effort to get a job done
- Uneven production and sales (mura)—peaks and valleys rather than a smooth, predictable workflow
- Unused talent—a good idea that went unspoken
On our farm we take muda elimination seriously. We look for the 10 mudas all the time. When we see them, as much as possible, we get rid of them. While muda is usually translated as “waste,” not all mudas are completely superflu-ous. We still file taxes, occasionally pull weeds, and send invoices to customers, even if these actions do not directly cause our products to be worth more. Not all mudas should be completely eliminated. The goal, rather, is to mini-mize the amount of time and energy given to non-value-adding activities.
We’ve come to realize that every activity we perform is either muda or value adding. There are no exceptions. Our job is to see the difference, and steer toward value. If we find ourselves performing a muda task, we ask, how can we shorten it or, better yet, eliminate it? As Shigeo Shingo, a Japanese engineer and arguably the world’s leading expert on manufacturing efficiency, observed, only the last turn of a bolt tightens it—the rest is just movement. We want to focus on bolt tightening, so to speak—on seeding, washing, harvesting, and selling—and minimize everything else. Cutting out muda has been a powerful force on our farm, increasing our profits every year, while we work less.
5. PRACTICE KAIZEN—CONTINUOUS IMPROVEMENT
The final step is to practice kaizen, or continuous improvement, rooting out more waste every year from the farm, and aligning production more tightly with customer demand. We have adopted the philosophy “When you fix it, fix it again.” Our goal is to create a farm culture where everyone on the team joins together in an effort to achieve zero-waste production.
Recommended Reads
Recent Articles
Storing seeds is the key to having a successful growing season. Follow these tips for keeping seeds organized so you’re ready to plant as soon as the time is right!
Read MoreEver wonder what worms and centipedes are doing as they crawl through your soil? They’re actually working to improve the soil’s health, which benefits the environment and all living things in the long run. The following is an excerpt from Farming on the Wild Side by Nancy J. Hayden and John P. Hayden. It has been adapted…
Read MoreLearn how to grow shiitake mushrooms in almost any environment, including your yard and even your garage!
Read MoreWinter may be coming, but that doesn’t mean you should put away those tools just yet! Extend the growing season past the first frost with a few modifications.
Read MoreWhat if we told you that there was a way to extend your growing season and save time & money? The answer is all in arugula. With quick hoops and greenhouse film, you’ll be on your way to harvesting sweet & flavorful arugula in no time. The following excerpt is from The Resilient Farm and…
Read More